在推動企業(yè)深化改革的進(jìn)程中,于凱杰同志勇挑重?fù)?dān),真抓實(shí)干,在技術(shù)攻堅(jiān)、管理革新等領(lǐng)域發(fā)揮著先鋒模范作用,為企業(yè)的高質(zhì)量發(fā)展做出了顯著貢獻(xiàn)。
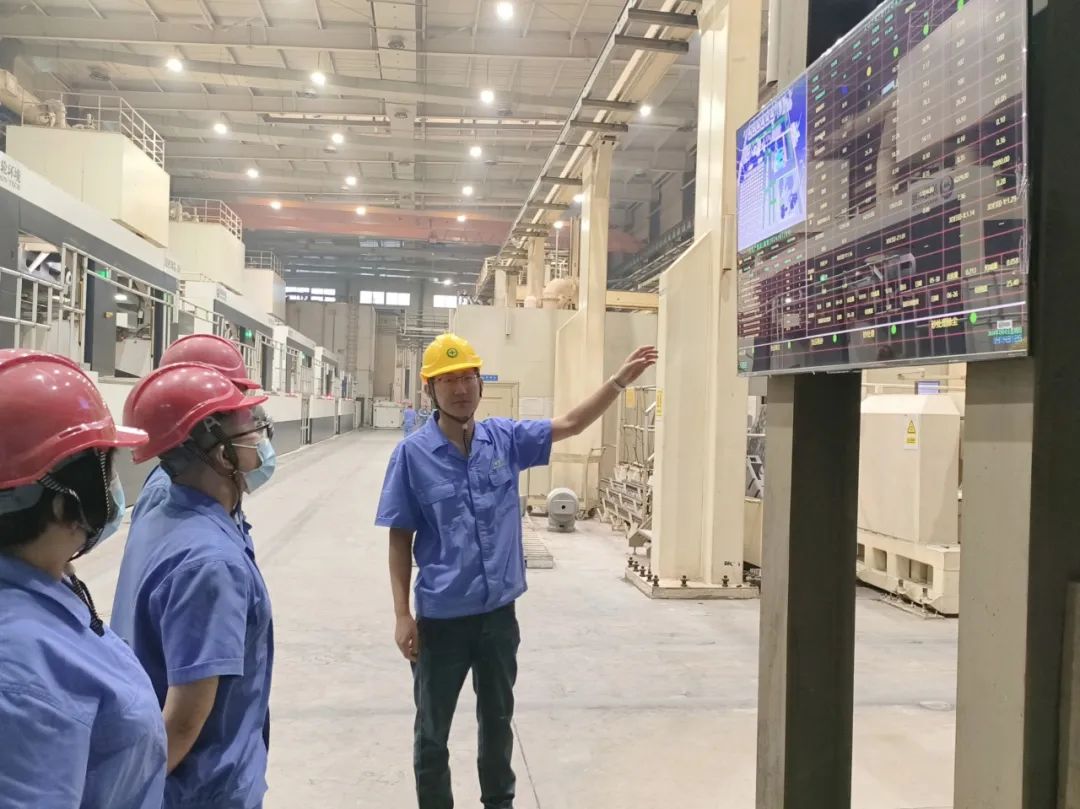
他憑借豐富的生產(chǎn)管理經(jīng)驗(yàn),精準(zhǔn)界定生產(chǎn)過程中各個(gè)環(huán)節(jié)的職責(zé)和操作規(guī)程,注重對質(zhì)量控制關(guān)鍵點(diǎn)的把控,顯著提升了產(chǎn)品質(zhì)量及生產(chǎn)效率。在他的帶領(lǐng)下,生產(chǎn)制造部始終高效率完成生產(chǎn)任務(wù),產(chǎn)品合格率穩(wěn)定保持在95%以上,超越行業(yè)平均水平,企業(yè)人均年產(chǎn)值約100萬元,遠(yuǎn)超同行業(yè)人均年產(chǎn)值。
他始終保持著敢于探索、勇于實(shí)踐的精神,順應(yīng)數(shù)字化時(shí)代發(fā)展趨勢,依托全球范圍內(nèi)全流程智能化水平最高的3D打印鑄造工廠,主動參與“砂型3D打印智能鑄造工廠全流程數(shù)字化生產(chǎn)系統(tǒng)及裝備研發(fā)與應(yīng)用”項(xiàng)目建設(shè),攻克多項(xiàng)技術(shù)難題,鑄造了新技術(shù)的產(chǎn)業(yè)化應(yīng)用,帶動產(chǎn)業(yè)鏈上下游的發(fā)展,推動行業(yè)進(jìn)步,引領(lǐng)中國鑄造轉(zhuǎn)型升級,實(shí)現(xiàn)綠色、智能鑄造。
為了使“砂型3D打印智能鑄造工廠全流程數(shù)字化生產(chǎn)系統(tǒng)及裝備研發(fā)與應(yīng)用”項(xiàng)目以先進(jìn)的全流程虛擬鑄造系統(tǒng)(VCS)為核心,與ERP、MES、LIMS等關(guān)鍵系統(tǒng)深度集成,實(shí)現(xiàn)從原材料采購、精細(xì)工藝設(shè)計(jì)到生產(chǎn)流程的全方位數(shù)字化管理,他連續(xù)奮戰(zhàn)40余日,使生產(chǎn)設(shè)備總數(shù)達(dá)88臺,數(shù)據(jù)采集率高達(dá)97%,其中76臺設(shè)備已成功實(shí)現(xiàn)組態(tài),組態(tài)率高達(dá)95%。整個(gè)系統(tǒng)共包含3900個(gè)變量,其中最為關(guān)鍵的生產(chǎn)過程參數(shù)達(dá)629個(gè),自動采集數(shù)量高達(dá)604個(gè),自動采集率接近96%。借助這一全流程智能鑄造系統(tǒng)平臺,公司實(shí)現(xiàn)了對生產(chǎn)設(shè)備的精準(zhǔn)管控,典型產(chǎn)品的設(shè)計(jì)周期縮短超過50%。此外,通過優(yōu)化流程,公司每年可節(jié)省人力資源成本105萬元,減少工裝費(fèi)用270萬元,同時(shí)降低廢品損失46萬元。相較于傳統(tǒng)的鑄造方式,人均產(chǎn)能更是提升了25%。這一卓越的項(xiàng)目成果不僅獲得了業(yè)界的廣泛認(rèn)可,更榮膺國家級8項(xiàng)實(shí)用新型專利與6項(xiàng)軟件著作權(quán)的殊榮。
作為一名共產(chǎn)黨員,于凱杰同志始終堅(jiān)持黨的原則,不忘初心,牢記使命,以高度的責(zé)任感和使命感,勇于攻克技術(shù)革新中的重重困難,他的工作軌跡就是對黨忠誠、勤奮工作、積極創(chuàng)新、勇于擔(dān)當(dāng)?shù)纳鷦訉懻铡?/p>